Enhancing efficiency in conveyor automation with Ultralytics YOLO11
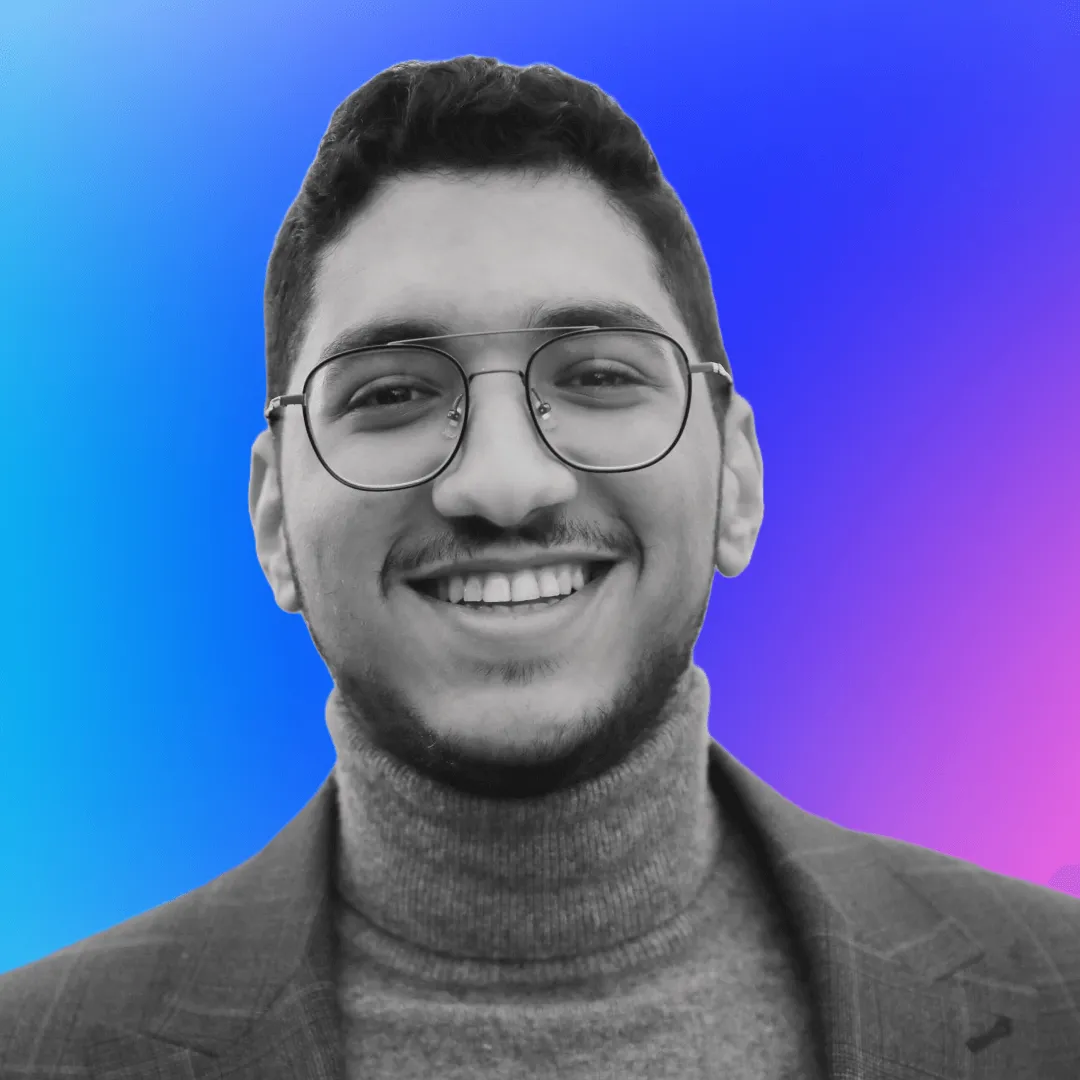
January 24, 2025
Learn how Ultralytics YOLO11 can enhance conveyor systems, streamline workflows, boost efficiency, and enable smarter solutions across industries.
.webp)
January 24, 2025
Learn how Ultralytics YOLO11 can enhance conveyor systems, streamline workflows, boost efficiency, and enable smarter solutions across industries.
Conveyor belts are the backbone of industrial automation, driving efficiency across sectors like manufacturing, logistics, food processing, and airports. Studies show that the global conveyor systems market is experiencing significant growth, driven by the increasing adoption of automation across various industries. In 2020, the market was valued at approximately USD 8.8 billion and is projected to reach USD 10.6 billion in 2025.
As industries evolve, the concept of "smart conveyor belts" is transforming how businesses operate. Integrating computer vision (CV) technologies like the Ultralytics YOLO models into conveyor systems enables companies to streamline processes with tasks such as real-time object detection, tracking, and counting.
The integration of artificial intelligence (AI) into conveyor systems is becoming increasingly important as industries look for ways to enhance efficiency and streamline operations. AI can contribute to improved workflows by optimizing efficiency, reducing waste, and supporting better decision-making.
Computer vision technologies help make conveyor systems better. They enable tasks like object detection for quality checks. They also assist in counting products for better resource management. This makes conveyor systems more effective and adaptable to industry needs.
In this article, we will explore the problems with traditional conveyor systems. We will see how Vision AI can help solve these issues, and discuss the steps to create a smart conveyor system. Finally, we will look at the benefits of using models like Ultralytics YOLO11.
Conveyor belt systems face several challenges that limit efficiency and productivity. Traditional methods often rely on manual monitoring or outdated systems that struggle with complex tasks. Here are some common hurdles:
These limitations highlight the need for smarter systems to adapt, automate, and improve operational efficiency—areas where computer vision and YOLO11 can contribute effectively.
Computer vision offers a more efficient and accurate alternative. High-resolution ai cameras integrated with computer vision algorithms can be trained to monitor conveyor belts in real-time, by performing tasks like object detection, tracking, and classification.
For example, in manufacturing, computer vision can detect defective products like scratched components or misaligned labels as they move along the belt. These items can be flagged for removal, ensuring that only high-quality products continue down the production line.
In logistics, packages can be automatically classified by size, shape, or barcode, making sorting faster and more accurate while reducing the risk of errors.
Integrating computer vision models like YOLO11 can enhance operational efficiency and enable industries to address challenges more quickly and effectively. By eliminating manual intervention and providing real-time insights, these systems help streamline workflows, reduce waste, and create smarter, more automated industrial processes.
So how can computer vision models help? YOLO11 stands out as a next-generation computer vision model, offering speed, accuracy, and flexibility. Its advanced features can make it well-suited for optimizing conveyor belt systems across diverse industries.
YOLO11's flexibility allows it to address the diverse requirements of modern industries, supporting the development of more efficient, AI-powered automation systems.
Now that we know why models like YOLO11 are helpful, let’s look at some common uses where they can help.
Conveyor systems are vital across numerous industries, and their optimization can have a significant impact on operational success. By integrating YOLO11, these systems can achieve enhanced efficiency, accuracy, and adaptability. Some key applications of YOLO11 in improving conveyor belt operations include:
In manufacturing, ensuring product quality is paramount. YOLO11’s object detection and instance segmentation capabilities can help identify defects on products moving along conveyor belts.
Imagine a factory producing canned beverages. YOLO11 can be trained to analyze each can as it passes along the conveyor belt, identifying defects such as dents, scratches, or misaligned labels. This enables manufacturers to remove defective cans from the production line before they reach packaging, reducing waste and improving overall product quality. YOLO11’s ability to handle high-resolution images ensures precise defect detection, even at high speeds.
The logistics industry serves as a critical link between manufacturers and consumers, relying heavily on speed and precision to meet growing demands. However, traditional methods often struggle with inefficiencies and human errors, particularly in fast-paced environments like distribution centers.
YOLO11 can offer a smarter approach to logistics by automating essential tasks such as package sorting and tracking. Using computer vision, YOLO11 can count and classify packages as they move along conveyor belts, distinguishing them based on size and shape. This enables real-time monitoring, ensuring each package is accounted for and routed accurately to its destination.
YOLO11 can be trained to detect damaged packaging enhancing quality control. For instance, it can flag torn or dented boxes, allowing operators to address issues before packages are dispatched. This level of automation not only improves operational efficiency but also enhances customer satisfaction by reducing delivery errors and delays.
Consider a scenario where YOLO11 is deployed in a bread production facility. As loaves move along the conveyor belt, YOLO11 can be used to count and track each loaf in real-time, ensuring accurate inventory records and smooth production flow.
It can also find problems, like foreign objects or visible defects on loaves, helping bakers keep high-quality standards. YOLO11’s monitoring capabilities can also help in detecting potential anomalies, contributing to improved food safety and reducing the risk of non-compliance with safety regulations.
YOLO11’s object-counting capabilities are particularly useful in bread production. By accurately counting each loaf as it passes along the conveyor, manufacturers can streamline inventory tracking and align production output with packaging operations. This ensures that there are no gaps or bottlenecks in the production line, optimizing efficiency and minimizing waste.
For example, the system can tally loaves in real-time, providing accurate data that can be used to streamline and update inventory records effectively. If a discrepancy arises, such as a sudden drop in the number of loaves detected, operators can quickly investigate and resolve the issue, ensuring smooth operations.
By leveraging YOLO11, food production facilities can enhance operational efficiency, ensure product quality, and meet industry safety standards.
Airports rely heavily on conveyor systems for baggage handling, and YOLO11 can enhance these systems by tracking and identifying luggage. Accurate baggage detection and counting benefit both airports and passengers by streamlining operations and reducing delays.
For instance, YOLO11 can accurately detect and count pieces of luggage as they move through the system. This enables airports to maintain real-time records of baggage flow, ensuring that all items are accounted for and reducing instances of lost luggage. By monitoring luggage counts, operators can identify bottlenecks and adjust workflows to keep operations running smoothly.
Passengers also benefit from reduced wait times and greater confidence in baggage handling processes. Automated systems powered by YOLO11 can contribute to improved customer experiences by ensuring luggage reaches its destination efficiently and securely.
Integrating YOLO11 into conveyor belt systems can offer several benefits:
Smart conveyor belts powered by computer vision models like YOLO11 are shaping the future of industrial automation. By enabling real-time object detection, tracking, and counting, YOLO11 enhances efficiency, reduces waste, and ensures high operational standards. Whether it’s improving quality control in manufacturing, streamlining logistics, or ensuring food safety, YOLO11 provides versatile solutions tailored to industry needs.
Join our community today and explore our GitHub repository to uncover the potential of AI. Discover AI applications in industries like manufacturing and healthcare on our solutions pages, and explore our licensing options to get started on your journey to smarter solutions!